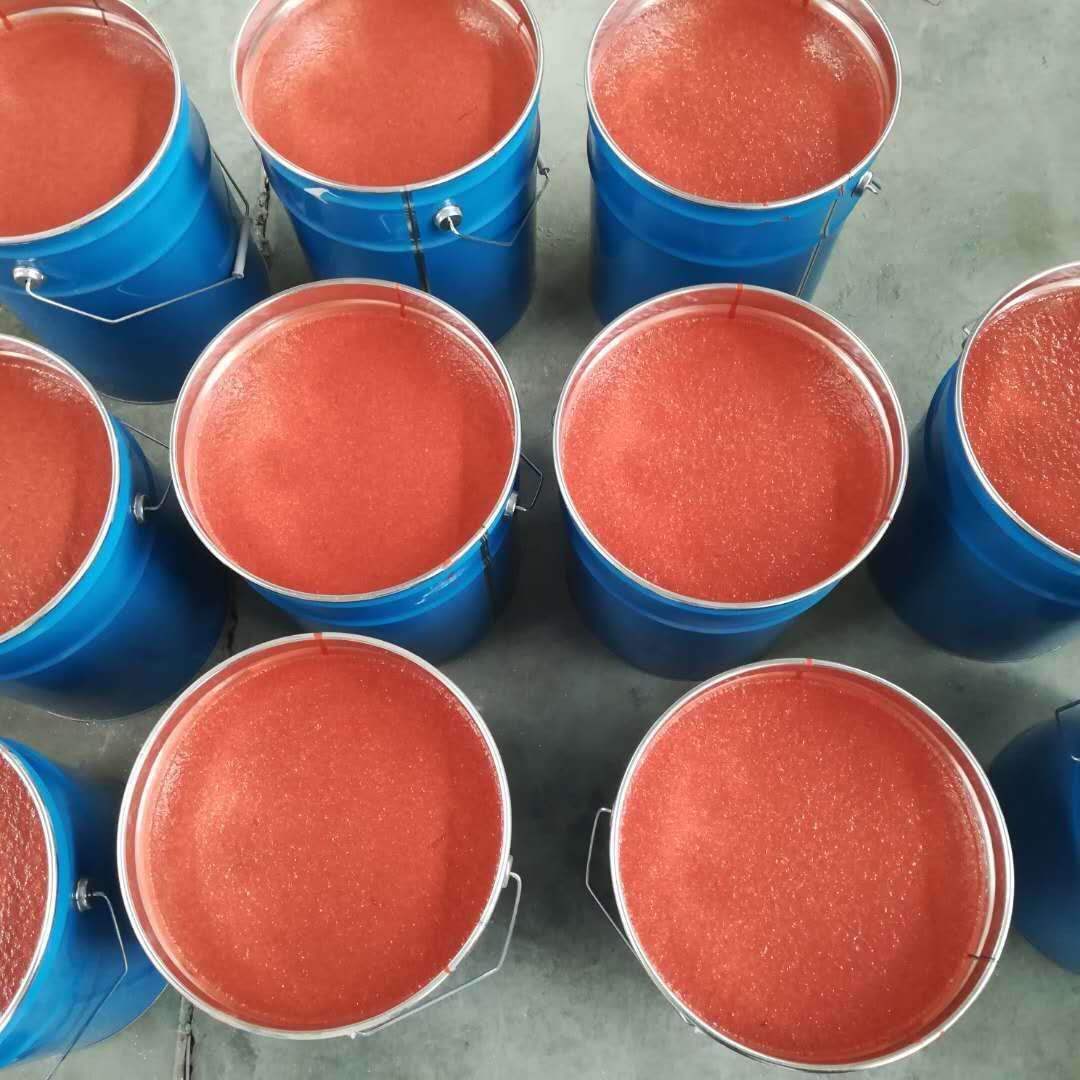
废水池用乙烯基玻璃鳞片涂料厂家
价格:11.00
乙烯基酯玻璃鳞片防腐施工方案1施工准备1.1管理策划准备根据该工程的特点,抓好施工准备工作。建立相应的施工***和管理制度,对该工程的施工过程进行控制和管理。开工前,***施工人员学习有关工艺规范、技术标准;进行工种培训;加强质量教育,使每个施工人员能自觉按规范和标准作业。1.2施工机械及检测仪器准备检测检测仪器,符合要求才能使用。投入该工程的设备有:(1)2台空气压缩机。压力为0.588~0.784MPa,配备后冷却器、油水分离器、砂罐等。(2)手提环保砂除锈机、电动砂轮。进行焊缝和焊伤处喷砂处理。(3)2台高压无气喷涂机。气漆体积比65∶1,同时去除所有的滤网;喷嘴压力15~25MPa;喷嘴可使用反转喷头,喷孔直径0.86~1.14mm、喷幅40°~80°,小面积区域或者预涂区域使用喷孔直径0.50mm的喷头。(4)防风机。保持施工环境的空气流通。(5)加热器。冬季施工时,将烟道内的温度加热到施工低温度15℃,平均温度应达到20℃以上。(6)除湿机。雨季施工时,降低烟道内的湿度。(7)高压水清洗机。(8)真空吸尘器。喷砂后、喷涂前,彻底清理钢管内表面的灰尘。(9)强力搅拌机。材料混合、搅拌。(10)检测仪器。测厚仪、钢材粗糙度仪、电火花检测仪、温湿度仪、湿膜卡。(11)其他。打磨机、吸尘器,漆膜保护材料,500ml量杯4个,红外温度计,苯已烯,,湿膜卡,电动搅拌器,5~10L的清洗小桶2个;施工人员保护设备;盖全脸的防毒面具。1.3施工场地准备及施工原材料准备根据现场施工需要,准备并保管好施工材料。喷砂涂装施工基地必须建在施工现场,场地应整空旷,面积约400m2,管材堆放、倒运、吊装应方便;电、水设施齐全。4.2乙烯基酯玻璃鳞片涂料的施工工序施工工序如图1所示。图1乙烯基酯玻璃鳞片涂料的施工工序4.3乙烯基酯玻璃鳞片涂料的施工方案4.3.1表面处理要求4.3.1.2表面预处理(1)喷砂前,用高压洁净水冲洗基材表面,将污染物如盐分、油污、油脂清洗干净;(2)喷砂前,用电动工具打磨底材表面的钻孔边缘、气割面及边缘、焊缝突起部分、焊渣及飞溅的焊点。这些部位应表面平整、圆滑过渡,以保证油漆能均匀覆盖钢表面。钢材的边角及边缘喷涂时,不能达到设计的漆膜厚度,必须用电动工具打磨成圆角(半径至少为2mm)。4.3.1.3表面喷砂处理采用钢丝切丸进行表面喷砂,步骤如下:(1)施工环境温度宜15~30℃,空气相对湿度小于85%,基体金属表面温度应大于***温度3℃以上。(2)钢结构表面及焊缝喷砂除锈时,要求除锈等级达到GB8923—88标准中规定的Sa2.5级,即喷砂后应无可见的油脂、污垢、焊渣毛刺、氧化皮、铁锈和油污、涂层等附着物,任何残留的痕迹应是点状或条纹状的轻微***;同时表面粗糙度为85~130μm。(3)喷射处理工艺参数。压缩空气工作压力为0.6~0.7MPa;喷射角,即磨料喷射方向与工作表面法线间夹角15°~30°;喷嘴离工件距离要求100~300mm;磨料粒径为0.5~1.5mm。(4)喷射所用的压缩空气必须经冷却装置及油水分离器处理,保证压缩空气清洁、干燥、无油。压缩空气应检查合格后方可使用,可将喷嘴对着白纸吹30s,不见油和水的痕迹,则可认为符合要求。(5)喷砂除锈后,喷涂前,用吸尘器表面浮尘和碎屑。清理后的表面不得用手触摸。涂装前,如发现钢板表面污染或返锈,应重新处理。4.3.1.4清洗油污及粉尘和喷涂底漆油污及粉尘用稀释剂清洗,清洁度达ISO8502—3中规定的2~3级以上。喷砂后,应及时喷涂底漆。因处理后的钢材表面容易返锈,一般应在4h内完成涂装底漆;潮湿环境下,应在2h内完成底涂。潮湿环境下,采用除湿机或加热器,以保持空气湿度符合标准(RH小于85%)。4.3.2喷涂施工要求4.3.2.1喷涂施工方法采用无气喷涂施工方式,施工方法如下:(1)涂装前,应将涂料各组分按涂料说明书配比、搅拌,搅拌均匀后方可喷涂。(2)对于边、角、焊缝、切痕等部位,喷涂前,应先人工涂刷1道,然后再进行大面积的涂装,以保证凸出部位的漆膜厚度。(3)喷涂厚度应均匀一致,该工程计划喷涂2道漆,干膜厚度为1200μm。在涂层未干实前,需防止浸水或雨淋。(4)喷雾扇面应尽量狭窄,喷涂距离通常为300~500mm,距离太小操作困难,容易出现流挂和皱皮;距离太大会造成涂膜表面粗糙且涂料损失增大。另外,喷与被涂表面应保持垂直。喷应在被涂表面平行移动,避免弧形移动。开始喷涂时,用湿膜测厚仪边测、边喷,确定移动速度,喷的移动速度以膜厚达到规定标准、又不出现流挂为宜。(5)喷涂设备连续喷涂1h后,应停止喷漆。需用专用稀释剂,在空载压力工况下,循环清洗喷涂机、高压软管、喷及喷嘴。(6)喷涂施工前,在每节钢管两端的管内壁预留出约150~200mm的焊接缝(实际宽度做实验后确定)。热影响区用胶带纸粘贴。(7)高压无气喷涂时,应保证喷涂机安全使用,高进气压力不准超过0.7MPa。喷涂过程中会产生静电,喷涂操作时,应将喷涂机接地,以防静电。喷涂过程中,当喷嘴不喷漆时,应清洗、更换喷嘴;这时,应及时将喷板机的***装置锁住。在任何情况下,喷口不能朝向自己或他人,以免误压板机,喷出高压涂料******。(8)只有在小面积预涂装或修补时,才可采取刷涂或辊涂。采用刷涂或辊涂时,漆膜厚度往往达不到设计要求。在一次涂装不能达到规定的干膜厚度时,必须采用多道施工方法,终达到规定的漆膜厚度。4.3.2.2施工的其他事项(1)空气、油漆、压力泵的温度;每次混合后,都要用清洗剂清洗、搅拌叶片;(2)清洗剂可采用、17号稀释剂或23号稀释剂;(3)施工将结束时,每次只准备1桶涂料待用。(4)如果在长期使用后,无气喷涂机反应迟缓或喷幅变小,此时应将已添加引发剂的油漆用完,再使用干净稀释剂清洗压力泵、喷管和喷。4.3.2.3施工时发生堵塞的处理(1)由于不完全雾化的油漆积在头表面,在喷头上引起堵塞时,用抹布或硬毛刷子沾些溶剂去擦洗头。(2)如果施工过程中,玻璃鳞片或不完全雾化的油漆在头后面引起堵塞,应取下头,放入盛有干净溶剂的容器内,换上干净的头,继续施工。(3)安装新头前,应先喷出少量的油漆,以保证管内油漆平滑流动。(4)如果缓冲器堵塞或流速缓慢,将泵减压后,取下缓冲器清洗。缓冲器取出后,压出少量的油漆,保证管内油漆流出正常。如果油漆流动缓慢或油漆干,则继续泵压油漆,直到油漆流出正常。(5)如果油漆流出正常,可用稀释剂清洗喷连接接口,更换新的缓冲器和头后继续施工。(6)如果油漆流出不正常,应立即清洗压力泵、流管和喷。(7)如果连续使用后,出现喷雾上、下晃动或喷气泵不发生敲击声,表明压力泵、流管和喷都需清洗。4.3.2.4设备的清洗移开油漆存放桶,洗刷干净吸漆管,将吸漆管放入一个盛满干净溶剂的清洁容器内,调低泵的压力,取下喷头后,将泵和流管内的剩余油漆泵出。当干净的溶剂流出后,换上喷头、继续压出,直到干净的溶剂流出。停止泵运转,将盛有溶剂的容器放在压力泵阀的下面。慢慢打开泵阀减压,启动泵,使溶剂循环流动约5min左右,直到泵发出均匀的敲击声。停止泵运转,关闭泵阀。从喷上取下头和缓冲器,放入溶剂中清洗。将喷放入溶剂桶内,慢慢重新启动压力泵,使溶剂回流循环。当溶剂循环流出物干净、顺畅时,停止压力泵运行。检查喷头和缓冲器是否干净,应没有玻璃鳞片粒子。在喷上重新装上缓冲器和头,所有连接接口应干净。启动压力泵,喷出油漆,保证整个施工系统清洁、没有粘连物。4.3.3涂装质量控制4.3.3.1油漆的准备(1)油漆放置一段时间后,会有不同程度的沉淀和分层。所以,开罐后,应电动搅拌,将其完全搅拌均匀后再使用,否则,将影响油漆的成膜品质。双组分油漆的主漆和固化剂混合后,有规定的使用时间。超过使用时间后,油漆会难以施工或不能施工。因此,要用多少漆就混合多少,以免造成浪费。(2)该产品混合后的使用时间短,在23℃的条件下只有45min。只有在所有的准备工作就绪以后,才能加入、混合引发剂和促进剂。4.3.3.2施工时的操作步骤(1)提前将2~3桶基料(如果用量许可)搅拌均匀,以保证基料供应的平稳持续性。(2)该阶段不要加入添加剂。(3)确保混合机干净,以保证在搅拌纯基料时,不受促进剂或杂质的影响。(4)测量气温、基漆以及压力泵体的温度,评估平均温度(要考虑压力泵摩擦产生的热量使温度)。(5)在确定平均温度后,准确计算促进剂、阻聚剂的数量。(6)正使用的漆桶,当桶内油漆用掉全桶3/4时,向准备的另外一桶漆内加入所需数量的1号引发剂。不要将新混合好的油漆直接加入正在使用的油漆中。(7)当桶内的油漆使用完后,迅速地将吸管抽出,插入准备的下一漆桶内。(8)将吸料管插入新漆桶内上、下各处,这样可避免空气阻塞。4.3.3.3基料、促进剂、阻聚剂及引发剂的配合比经过严格计算和实际测试,得出佳配合比、材料的混合比及混合后的使用时间,见表1。4.3.3.4涂装施工的环境条件控制施工前,前道涂层的表面要清洁、干燥,且底材温度要高于***温度3℃以上,以免底材结露影响涂料的附着力。雨雪天施工时,用防雨布覆盖管口,避免雨雪淋湿防腐层,特别是已安装的37m钢内筒,施工时,上口一定要用防雨布遮盖。施工环境条件应满足以下标准:(1)ISO8502—4规定。油漆施工前,钢材表面可能发生结露的评估指导。底材温度应为15℃以上,适合的温度为23℃(不能超过40℃)相对湿度在85%以下,应在施工区域内测量;底材温度至少高于空气***温度3℃。(2)ISO2808规定。油漆膜厚的确定。(3)NACERPO188—88规定。400Vμm,推荐用电子***探测仪在第1道油漆后检测。考虑到环境温度达不到涂料固化对环境温度的要求,所以,在涂料喷涂施工前,需在钢管内部进行加热,温度升至35℃左右,且该温度要一直保持到所有涂层固化为止。加热器采用3~4台安全系数高的油式电加热器(2000W)。为了达到更好的加热效果,钢管上口加热时需用防火布覆盖。4.3.3.5漆膜厚度的控制(1)施工时,必须检查湿膜的厚度,做到对所喷的干膜厚度可进行大致的预测。施工各道油漆时,要注意使漆膜均匀,并达到规定的漆膜厚度。(2)用湿膜卡、干膜测厚仪检测漆膜的厚度。(3)湿膜的检测方法:油漆喷涂后,应立即用湿膜测厚然后取出湿膜卡,读取数值。(4)湿膜厚度与干膜厚度的相应值为干膜厚度600μm;湿膜厚度625μm;理论涂布率为1.6m2/L。涂装的膜厚度标准要求达到1200μm。膜厚控制应遵守2个90%的规定,即90%的测点应在规定膜厚以上,余下的10%的测点应达到规定膜厚的90%。测点密度根据施工面积定。4.3.3.6涂装间隔期一道漆涂装完毕后,在进行下道漆涂装之前,要确认是否已达到规定的涂装间隔时间,并且在涂装间隔时间内,否则就不能进行涂装。不同温度下的涂装间隔时间见表2。表2在不同温度下的涂装间隔时间4.3.3.7漆膜的完全固化漆膜表干、硬干后,尚不能使用,必须完全固化后,才能使用。烟道内应避免机械碰撞或机械擦伤等损伤漆膜。环境温度越高,完全固化时间越短;反之,环境温度越低,完全固化时间越长。4.3.4安装焊缝处的喷涂及缺陷修补(1)涂装缺陷、***、漏涂、焊缝和碰伤、擦伤等应修补。(2)修补的区域应干燥,无油脂、无杂质。(3)待修补区域应除去防腐层的松散部位,表面除去修补区域的焊瘤、毛刺和其他污物,补口处应保持干燥,然后采用手提式喷砂机处理,质量应达到GB/T8923—1988规定的Sa2.5级。(4)根据涂料固化对环境温度的要求,在环境温度达不到要求时,焊缝处及修补区域需加热,采用红外线加热,即喷涂钢管外壁缠绕红外线加热绳(6道),使钢管壁温度加热达到30℃左右,并持续恒温2h至涂层实干。(5)在焊口清根时,要对防腐层实施保护,避免焊接火花***防腐层。(6)由于焊缝处的喷涂及缺陷修补在高空进行,所以该处施工是该工程的安全隐患之处。经研究,决定采用吊篮代替普通脚手架进行高空作业。吊篮制作和安装由***人员进行。5质量检查成品管的检验应严格执行ST/Y0414—98标准和油漆企业施工标准,检验项目包括防腐层外观、厚度、电火花检漏。)