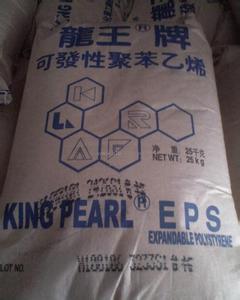
龙王牌EPS B-4S
产品参数EPS塑料特性、成型工艺、用途▲EPS操作过程EPS加工一般都经过预发泡、圆熟、成型、产品熟化这几道工序A、发泡原料珠粒在连续式或间歇式预发机内被蒸汽加热至92℃以上时软化,发泡剂挥发逸散粒子体积缓缓膨胀为所需倍率或克重。稳定的倍率是获得固定成型条件的保证,成型品质才能得以保障,由于预发条件不尽相同,故必须依赖操作人员的熟练和经验,在允许发泡速度内,适当调整预发温度、蒸汽压力、进料量和发泡倍率以获得满意的结果。B、圆熟刚发好的泡粒因发泡剂蒸发和残留发泡剂冷凝,内部呈真空状态而显软而没有弹性,因此必须有充分时间让空气进入泡粒内部微孔使之内外压力平衡而富弹性,一般需4小时左右,为提高制品质量,在条件允许下可延长时间,进行二次发泡圆熟2-3小时可进行第二次发泡。圆熟宜在用网状防静电纱布制成的圆熟仓内,以利附著于泡粒水分散发和消除泡粒摩擦时自然积留的静电,同时通风良好能增加圆熟程度。为避免刚发的泡粒尤其发得很轻的泡粒在风送时被碰瘪和冷风使泡粒收缩而陡增圆熟时间,以泡粒自由落进仓内为佳,若条件允许可待泡粒稍圆熟后再风送或风吸至料仓可获得饱满的泡粒,并可减少同熟时间。C、成型圆熟之后泡粒在一定模具填充后被蒸汽加热可融结成固定形状的成型品,具有韧而轻密融结,密闭泡孔不吸水的特性。加工成型的条件或操作不当,会导致成品收缩、表面不平、脱模不易、产品发脆、废品率高等不良现象。蒸汽、冷却水、压缩空气供应条件是保证产品脱模好、结合性佳、表面漂亮及缩短成型周期的基础,因此必须稳定。主蒸汽压力:0.4-0.7Mpa冷却水压力:0.3-0.5Mpa压缩空气:0.45-0.70Mpa真空度:-600-650mmHg操作人员丰富的经验是生产良好产品的关键,能对一个产品制定出相应的操作参数并根据产品的情况作相应的参数调整,以达到产品的完美。D、产品熟化脱模出来的产品表面附着水份及产品泡粒蒸汽凝结成水份须以蒸发,同时产品泡粒呈真空状态以及因冷减压产生较大收缩力,较高倍率产品可能在薄壁部分产生收缩,因而需要熟化,经仓库放置或太阳晒后的成品硬度和强度都会提高,若能在50-60℃的烘房内熟化则更好。▲储存注意:1.EPS储存场所应以阴凉通风良好为宜,为防止发泡剂逸失过快,保持适度倍率,储存室温以25℃以下为佳,并时常保持通风。2.EPS含有可燃挥发性发泡剂,在储存状态下也会缓解,故原粒、泡粒或成型品场所严禁烟火、静电或闪电发生,以免危险。3.原料尽量先进先用、保持新鲜,才能获得稳定的操作条件和良好的产品。▲EPS加工生产过程中常见弊病和原因及改善方法:EPS加工技术和工艺在国内已日趋完善和成熟,但是随着同行竞争越来越激烈,利润越来越薄,EPS加工厂家纷纷降低生产成本和提高产品质量以求胜出,这就需要EPS加工厂家重视生产加工中的每一个环节,就加工生产过程中的弊病进行分析和改善,以达到目的。EPS加工生产过程中常见弊病、原因、改善方法列举:(供参考)<TDclass=css序号加工程序不良状况原因改善措施Ⅰ预发泡A.泡粒结块1.原粒涂层剂太少1.原粒增拌涂层剂2.原料内有细粉2.使用粒度均匀之原料3.蒸汽压力太高3.调低蒸汽压力,加减压阀4.发泡温度高4.调低发泡桶内温度5.蒸汽含水太多5.蒸汽管路加疏水器6.发泡桶底部冷凝水排放不畅6.发泡机冷凝排放管线通畅7.加料速度慢,桶内滞留时间长7.增加加料速度8.原粒过期,倍率不足8.用做发低倍率料B.预发泡粒潮湿1.蒸汽太潮湿1.蒸汽管路保温,设疏水器2.预发机顶盖通风不良2.改进蒸汽逸散风管3.预发机保温不良3.预发泡机保温不良C.泡粒受缩1.预发倍率太高1.根据不同类别确定发泡倍率2.蒸汽压力太高,温度高2.用二次发泡未获得较高倍率,调整降低蒸汽压力3.天气特冷或温度太低3.空气温度低,增设流化床或用热风送料4.泡粒在发泡桶内滞留时间太长进料4.增加进料速度或适当调低泡粒出口挡板太少D.倍率不稳定1.进料速度不匀1.1原料湿,晾干1.2螺杆送料系统疏通2.蒸汽压力不稳定2.检查蒸汽管线,增加减压阀稳定蒸汽压力3.新旧原料,不同料别掺和3.尽量使用同种同批原料E.预发工程有未发粒子团出现1.发泡机清理门未关死1.关紧底部清理门2.发泡机搅拌速度太快2.合理调低搅拌速度3.进料速度太快3.合理调低进料速度4.发泡温度偏低4.合理调高发泡温度F.P料多次发泡倍率低1.原料发泡剂含量偏低1.更换原料2.第一次发泡收缩2.保证第一次发泡不收缩,调整蒸汽和压力3.多次发泡之间间隔太长与太短3.合理缩短与延长间隔时间A.泡粒打瘪破损变形,密度增加1.鼓风机风力太小1.合理选择鼓风机功率2.输送管线弯角太多2.合理布置、尽量减少弯角3.输送管径太小3.增加管径,150mm较合理4.泡粒经过风机叶抽打输送4.改为不经风叶之喷送式送泡粒Ⅱ泡粒输送B.输送泡粒管易堵塞1.管径太小1.增大管径,合理布置2.泡粒太湿2.增设流化床3.操作不当3.每次开机送粒或停机必须将输送管中泡粒吹空方可实行送粒或停机Ⅲ熟化A.熟化效果差1.熟化仓(料仓)区域通风不1.改善送风,增设排风系统良,且环境潮湿温度低2.有条件可通干燥热风,合理熟化2.熟化仓太大仓太小B.熟化仓带静电大(易引致火灾)1.熟化仓选材不当,如用木制1.采用自然水管等导电材料作支架品作支架2.接地不良2.将所有料仓引接地线C.熟化仓有死角泡粒滞留1.熟化料仓底部倾斜角度不够1.增加熟化料仓底部倾斜角度2.熟化料仓带静电2.选用导电材料作支架,并接地Ⅳ成型A.结合性不良1.加热时间不够1.延长加热时间2.蒸汽过热,压力过高2.改过热蒸汽为饱和蒸汽降低蒸汽压力3.泡粒圆熟时间太长3.缩短圆熟时间在24小时内4.泡粒水份太高4.1吹风晾干或热风吹干5.蒸汽压力太低4.2适当延长圆熟时间6.涂层剂太多5.适当调高蒸汽压力7.模具不良6.更换原料7.1模具蒸汽孔太少7.①增加模具蒸汽孔7.2模具蒸汽孔堵塞7.②模具蒸汽孔堵塞,则疏通7.3长久使用未清理7.③模具蒸汽室是否积垢,清理7.4模具密封不够,漏气7.④模具密封更换密封条8.合模间距太大8.选适用之原料,减少合模空间B.脱模不良1.加热太久,粘模1.缩短加热时间2.温度太高2.降低蒸汽压力3.冷却不够3.增加冷却水量,延长冷却时间4.模具不良4.①增加脱模斜度4.1脱模斜度不足4.②提高型芯,模具表面光洁度,4.2型芯,膜表面粗糙如有条件可进行涂铁氟层4.3顶杆布置不当4.③顶杆布置合理,用力平衡4.4模具蒸汽孔受损,粘膜4.④更换蒸汽孔5.空气压力不足5.检查压缩空气压力,并调整C.成型品表面收缩1.加热太久,温度太高,烧伤1.降低蒸汽压力,缩短加热时间2.冷却太快,水伤2.①提高冷却水水温2.②减少冷却水量2.③延长冷却时间2.④尽量以真空冷却为主,水冷为辅3.进料不足或不均3.①合理布置料仓位置3.②检查料仓是否受堵3.③提高进料压力,延长进料时间3.④增加模具合模间隙3.⑤改用较小粒度原料4.锁模力小够,模具密封向加热突然泄漏4.调整模腔压力低于锁模力5.泡粒圆熟时间不足5.延长圆熟时间6.发泡倍率太大6.调整发泡倍率D.成型品膨胀或变形1.泡粒圆熟不足1.延长圆熟时间2.发泡发率太大2.调整发泡倍率3.加热不均3.检查模具蒸汽孔4.冷却不足或不均4.增加冷却时间,检查冷却孔分布,增加冷却水量5.环境温度低5.减少与冷空气接触时间设烘房)