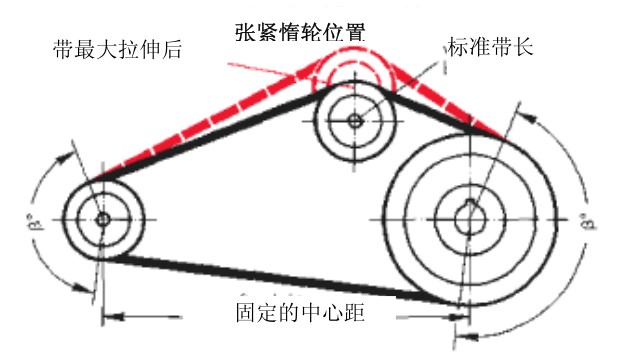
Continental ContiTech马牌同步皮带在单出杆液压缸液压回路伺服系统的制作方法
目前,单出杆液压缸液压回路中,通过节流阀或者泵的容积调节来实现执行机构速度与动力源输出流量之间的匹配关系,能满足基本实用要求。但是节流调速系统发热量大,效率低,系统噪声大,体积庞大;泵的容积调速系统结构复杂,对油液要求较高,电机空转损耗大。虽然已有电机泵一体化技术、变频容积调速技术、伺服电机泵技术解决传统液压动力源低效率、高能耗、高冲击的问题。但由于单出杆液压缸的两腔容积差,难以实现闭式或半闭式的无阀回路,一般还是使用传统的定量泵阀控回路或者变量泵泵控回路。伺服电机泵在注塑机上有成功应用,但是由于吸油压力的限制,伺服电机无法做到双向旋转,回路中仍然需要配置节流阀、换向阀等控制阀,仍然存在节流损失和换向冲击。ContinentalContiTech马牌公司发明的目的就是为了克服现有技术中的不足,提供一种应用于单出杆液压缸压机的直驱式电液伺服系统,采用马牌同步带、伺服电机驱动双向定量泵的变转速容积调速原理,通过压力反馈、位置反馈闭环控制伺服电机转速来改变双向泵的输出流量,以适应重力下拉式单出杆液压油缸活塞杆在各种工况下的速度,使用半闭式的液压回路,避免了使用节流调速和溢流调压、保压的大量能量损失;使用泵控的无阀回路,避免了换向冲击。ContinentalContiTech马牌发明的目的是通过如下技术措施实现:一种应用于单出杆液压缸压机的直驱式电液伺服系统,它包括信息采集系统、同步带、控制器、伺服驱动器、伺服电机、双向定量泵、液压缸、油箱,其中,液压缸为重力下拉式单出杆液压缸;所述信息采集系统包括有杆腔压力传感器、无杆腔压力传感器和活塞杆位移传感器,ContinentalContiTech马牌所述有杆腔压力传感器连接至液压缸的有杆腔,无杆腔压力传感器连接至液压缸的无杆腔,所述活塞杆位移传感器通过螺纹连接于液压缸尾端;其中,有杆腔压力传感器用于采集连接至液压缸的有杆腔的油路压力值,无杆腔压力传感器用于采集连接至液压缸无杆腔的油路压力值。所述控制器的信号输入端分别与有杆腔压力传感器、无杆腔压力传感器、活塞杆位移传感器连接同步皮带;用于接收有杆腔压力传感器采集的压力值信号、无杆腔压力传感器采集的压力值信号、活塞杆位移传感器采集的液压缸活塞杆的位移信号,并产生伺服电机驱动指令信号。所述伺服驱动器的信号输入端与控制器的信号输出端连接,其输出端与伺服电机连接。所述伺服电机与伺服驱动器的UVW输出端连接;所述控制器向伺服驱动器输出伺服电机驱动指令信号,所述伺服驱动器根据伺服电机驱动指令信号控制伺服电机的动作。ContinentalContiTech马牌所述双向定量泵的油口A与液压缸的无杆腔连接,油口B经***电磁阀控制的二通插装阀与液压缸的有杆腔连接。所述油箱经吸油过滤器和液控单向阀与双向定量泵的油口B连接,油箱经充液阀且并联***单向阀与液压缸的无杆腔连接。所述液压缸的无杆腔通过充液阀连接油箱。当活塞杆下行,且只有活塞杆自身重力和压头重力负载,油箱经单向阀和充液阀向油缸无杆腔补油;当活塞杆上行,无杆腔的多余油液经充液阀和回油过滤器回到油箱。ContinentalContiTech马牌在上述技术方案中,所述油箱安装在一个5至20米高的塔架或平台上,增加了油箱到双向泵油口B的压力,能够满足其较高转速下的自吸压力。在上述技术方案中,在系统流量较大的应用场合,液压缸的有杆腔和无杆腔经起通断作用的第二电磁阀连通,形成差动回路。在液压缸无杆腔连接的充液阀关闭,双向泵的油口B经液控单向阀和吸油过滤器从油箱吸油时,控制差动回路通断的第二电磁阀开启,有杆腔的油液回到无杆腔。ContinentalContiTech马牌上述技术方案中,从油箱到双向定量泵的油口B的吸油管路上安装有吸油过滤器,从液压缸到油箱的回油管路上安装有回油过滤器,吸油过滤器为粗过滤回油过滤器为精过滤,ContinentalContiTech马牌上述技术方案中,双向定量泵的油口A连接液压缸的无杆腔的油路经第二单向阀和安全阀连接到油箱;油口B连接液压缸的有杆腔的油路经过第三单向阀和安全阀连接到油箱。在上述技术方案中,在液压缸的活塞杆的行程中设置有四个位置可调的行程开关,行程开关的信号输出端与控制器连接,ContinentalContiTech马牌在上述技术方案中,伺服电机上设有编码器,伺服驱动器的信号输出端与伺服电机的编码器连接。与现有技术相比,本发明的有益效果在于:采用变转速容积调速原理,通过压力反馈、位置反馈实现闭环控制伺服电机转速,实现不同工况下泵的输出流量与液压缸活塞杆的速度匹配,减少系统的节流和溢流损失。活塞杆的速度可以无级调节,在系统启动瞬间、活塞杆增速和减速瞬间,通过控制电机的加速度曲线可以***大程度降低系统的冲击噪声。通过伺服电机和双向定量泵的正反转实现油缸活塞杆的换向,避免使用换向阀而产生换向冲击。将闭式回路应用于重力下拉式单出杆液压缸,实现了不依靠补油泵和压力油箱对液压缸和泵进行补油,同时也减少了回油量,缩小了所需油箱的体积。在活塞杆自由下落阶段,电机处在发电工况,通过电源回馈或者耗散电阻转移该部分能量,避免了使用节流阀而使液压系统发热。在保压和卸荷阶段,通过压力反馈控制,液压泵几乎可以停机,极大程度减小了系统的溢流损失。泵控无阀回路的应用,减少了控制阀的数量,降低了系统的故障率。经试验和仿真计算表明,该系统相比于异步电机驱动单向定量泵的阀控节流溢流系统,效率提升80%左右,节能超过70%,冲击噪声降低60%-90%,可广泛应用于烟片预压打包机、注塑机、锻造机、升降平台等。附图说明图1是本发明应用于单出杆液压缸压机的直驱式电液伺服系统的原理框图。其中,1、第三单向阀;2、安全阀;3、双向定量泵;4、第二单向阀;5、液控单向阀;6、伺服电机;7、***电磁阀;8、有杆腔压力传感器;9、第二电磁阀;10、马牌同步皮带;11、***单向阀;12、充液阀;13、吸油过滤器;14、活塞杆位移传感器;15、回油过滤器;16、无杆腔压力传感器;17、二通插装阀;18、伺服驱动器;19、液压缸;20、***行程开关;21、控制器;22、信息采集系统;23、编码器;24、第二行程开关;25、第三行程开关;26、第四行程开关。具体实施方式为了使ContinentalContiTech马牌发明技术特点、特征、技术效果、设计目的更易于理解,下面结合图例对本发明做进一步阐述。ContinentalContiTech马牌发明实施例提供一种应用于单出杆液压缸压机的直驱式电液伺服系统,它包括:息采集系统22,所述信息采集系统22包括有杆腔压力传感器8、无杆腔压力传感器16和活塞杆位移传感器14。其中,有杆腔压力传感器8用于采集连接至液压缸19的有杆腔的油路压力值,无杆腔压力传感器16用于采集连接至液压缸19无杆腔的油路压力值。控制器21,所述控制器21的信号输入端分别与有杆腔压力传感器8、无杆腔压力传感器16、活塞杆位移传感器14、行程开关连接,用于接收有杆腔压力传感器8采集的压力值信号、无杆腔压力传感器采集16的压力值信号、活塞杆位移传感器14采集的液压缸活塞杆的位移信号和行程开关采集的活塞杆位置信号,并产生伺服电机驱动指令信号。伺服驱动器18,所述伺服驱动器18的信号输入端与控制器21的信号输出端连接,其输出端与伺服电机6的编码器23连接。伺服电机6,所述伺服电机6与伺服驱动器18的UVW输出端连接。控制器21向伺服驱动器18输出伺服电机驱动指令信号,伺服驱动器18根据伺服电机驱动指令信号控制伺服电机6的动作。双向定量泵3,所述双向定量泵3的油口A与液压缸19的无杆腔连接,油口B经***电磁阀7控制的二通插装阀17与液压缸19的有杆腔连接;油箱10经吸油过滤器13和液控单向阀5与双向定量泵3的油口B连接,经充液阀12且并联***单向阀11与液压缸19的无杆腔连接。液压缸19,所述液压缸19为重力下拉式单出杆液压缸,所述液压缸19无杆腔通过充液阀12连接油箱10,当活塞杆下行,且只有活塞杆自身重力和压头重力负载,油箱10经***单向阀11和充液阀12向液压缸19无杆腔补油。当活塞杆上行,无杆腔的多余油液经充液阀12和回油过滤器15回到油箱。油箱10,所述油箱10安装在一个5至20米高的塔架或平台上,增加了油箱10到双向定量泵3油口B的压力,能够满足其较高转速下的自吸压力。为了使系统适应流量较大的应用场合,液压缸19的有杆腔和无杆腔经起通断作用的第二电磁阀9连通,形成差动回路。在液压缸的无杆腔连接的充液阀12关闭,双向定量泵3的油口B经液控单向阀5和吸油过滤器13从油箱10吸油时,控制差动回路通断的第二电磁阀9得电,***电磁阀7失电,有杆腔的油液回到无杆腔。为了不依靠补油泵或者压力油箱弥补单出杆液压缸的两腔容积差,采用更为简单的自吸油补油技术,将油箱10安装在5至20米高的塔架或平台上,分两路对系统进行补油:一路为油箱10经***单向阀11和充液阀12到液压缸19的无杆腔;另一路为油箱10经吸油过滤器13和液控单向阀5到双向定量泵3的油口B。为了对油液中的杂质进行过滤处理,从油箱10到双向定量泵3油口B的吸油管路上安装有吸油过滤器13,从液压缸19到油箱10的回油管路上安装有回油过滤器15。为减小吸油压力损失,吸油过滤器13为粗过滤;为保证系统的过滤精度,回油过滤器15为精过滤。液压缸19无杆腔吸油时回油过滤器15中的止回阀关闭,***单向阀11开启;液压缸19无杆腔回油时,回油过滤器15中的止回阀开启,***单向阀11关闭,一部分油液经过双向定量泵3回到有杆腔,一部分经回油过滤器15回到油箱。为了防止系统在某些突发情况下过高的压力峰值对油路中元器件和接头产生损害,双向定量泵3油口A连接液压缸19无杆腔的油路经第二单向阀4和安全阀2连接到油箱10;油口B连接液压缸19有杆腔的油路经过第三单向阀1和安全阀2连接到油箱10。为了在停机或者待机状态下,将液压缸19的活塞杆和压头悬挂在上位,在有杆腔到双向定量泵3油口B的油路上连接有***电磁阀7控制的二通插装阀17。为了保证活塞杆在运动过程中具有一致性的加速段、减速段、快速运行段和慢速运行段,在液压缸19的活塞杆的行程中依次设置有四个位置可调的行程开关20、24、25和26。行程开关的信号输出端与控制器21连接,以便控制器21根据活塞杆的位置发出不同的伺服电机转速控制指令。伺服电机6上设有编码器23,编码器23具有接收伺服驱动器18发送来的转速控制指令和反馈伺服电机当前转速信号的功能。ContinentalContiTech马牌发明的工作原理如下:系统的初始状态为:伺服电机6转速为0,***电磁阀7失电,二通插装阀17处在关闭状态,第二电磁阀9失电,差动回路断开,液压缸活塞杆处在收缩状态,压头悬挂在上位。系统开始工作时,***电磁阀7得电,二通插装阀17开启。为了避免启动冲击,伺服电机6以一定的加速度启动,液压缸19的有杆腔油液经由双向定量泵3回到无杆腔。由于两腔容积差,无杆腔形成负压,充液阀12和***单向阀11开启,油箱10向无杆腔补油。该阶段活塞杆和压头自由下落,通过伺服电机6的转速控制其下行速度。当压头接触到被压缩物,被压缩物对压头的反向作用力逐渐增大,液压缸19有杆腔的压力逐渐减小,直到液控单向阀5开启,油箱与双向定量泵3油口B连通;液压缸19无杆腔的压力逐渐增大,直到充液阀12关闭。双向定量泵3经液控单向阀5和吸油过滤器13从油箱吸油。第二电磁阀9得电,***电磁阀7失电,差动回路连通。有杆腔压力随着被压缩物的体积减小逐渐增大,系统进入慢压阶段。特别的,在系统流量不是很大的应用场合,可以取消第二电磁阀9控制的差动回路,且在该阶段保持***电磁阀7得电。在慢压阶段,信息采集系统实时获取液压缸19的两腔压力,控制器21根据液压缸19的无杆腔压力值输出伺服电机转速控制信号,形成压力反馈闭环控制。当压头下压到第三行程开关25所处的位置,控制器21开始对伺服电机6进行减速,直至压头到达第四行程开关26所在位置,电机停止转动,形成位置反馈闭环控制。压头下行到第四行程开关26所在位置时,伺服电机6停止转动,由于泵、油缸等的泄漏,无杆腔压力逐渐减小,压头位置出现缓慢反弹。根据信息采集系统22,控制器21输出伺服电机转速控制信号,使系统压力和压头位置重新回到既定水平,伺服电机再次停机。通过上述动作的循环,可以实现系统的无溢流保压。保压结束后,第二电磁阀9失电,***电磁阀7得电,伺服电机6反转,液压缸19有杆腔压力通过控制油路将充液阀12开启;无杆腔一部分液压油经充液阀12和回油过滤器15回到油箱10,一部分液压油经双向定量泵3和二通插装阀17回到有杆腔。在压头上行到第三行程开关25所处位置前,活塞杆和压头慢速上行;在压头上行到第三行程开关25所处位置后,活塞杆和压头快速上行;在压头上行到第二行程开关24所处位置后,活塞杆和压头减速慢行;在压头上行到***行程开关20所处位置时,***电磁阀7失电,伺服电机6停止转动,系统回到初始状态。ContinentalContiTech马牌以上所述的具体实施实例,仅为本发明的较佳实施方式之一。除此之外,本发明还可以有其他实现方式。需要说明的是,凡在本发明的精神和原则之内所做的任何修改、等同替换、改进等,均应包含在本发明的保护范围之内。)