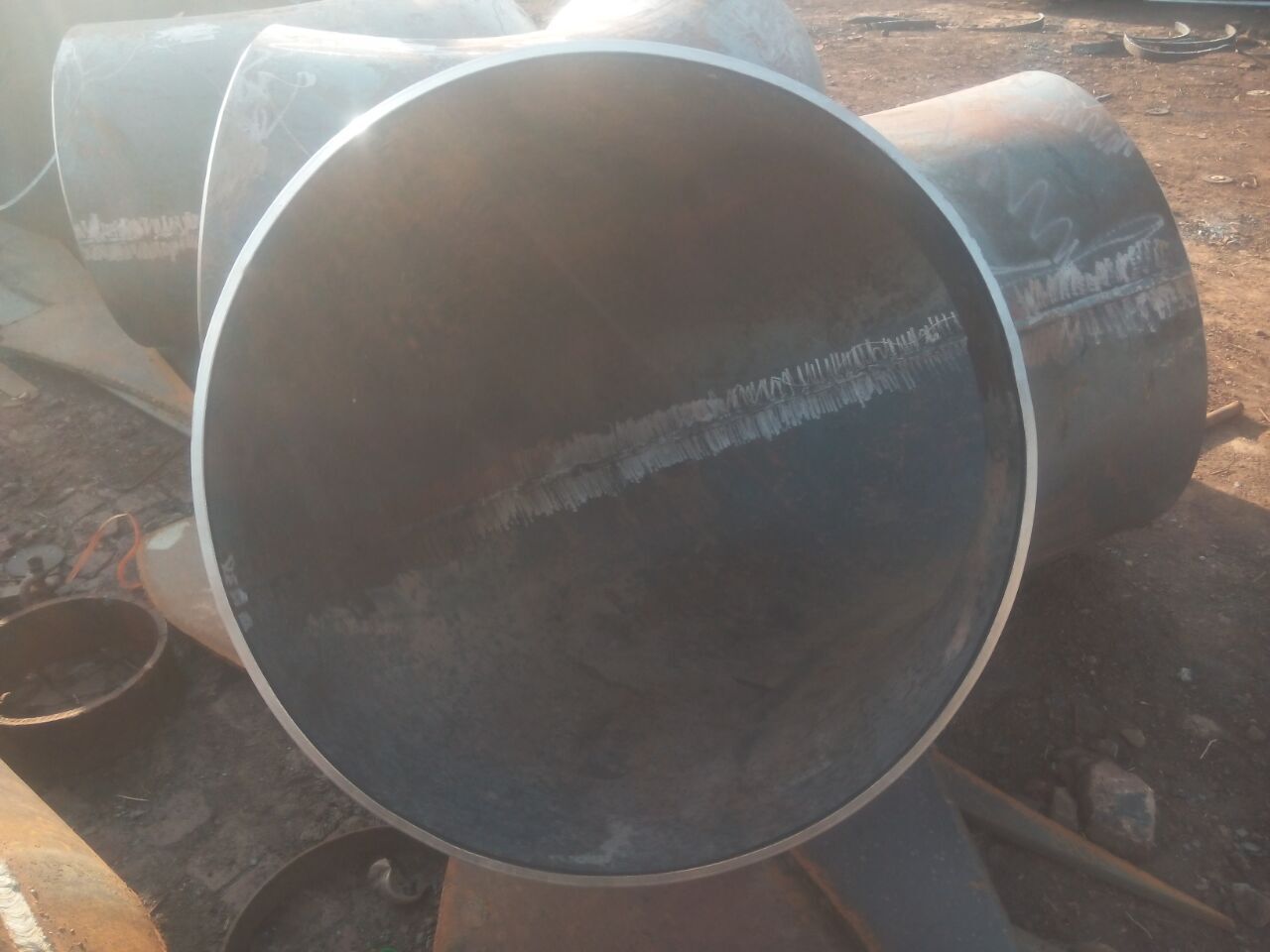
90度碳钢厚壁弯头生产厂家
价格:99.00
河北晟拓管道装备有限公司(杨经理:139晟317拓30975)国标高压弯头为获取上游弯头安装前提对内锥流量计的机能影响和所需的*短直管段长度,应用计算流体动力学数值仿真,对100mm口径,等效直径比的内锥流量计开展了上游单90°弯头的仿真研究.仿真介质为常温水,雷诺数范围:研究方案分基线和上游单90°弯头两类,共15组.利用均匀流出系数相对误差及附加不确定度作为安装前提的主要评价尺度,给出了上游单个90°弯头的直管段长度,并与国外研究结论作了比较.国标高压弯头适用于石油、***、化工、水电、建筑和锅炉等行业的管路系。高压弯头的用途与安装用途:高压弯头用于管道拐弯处的连接.连接两根公称通径相同的管子,使管路作角度转弯.以材质划分高压弯头,铸钢弯头,合金钢弯头,不锈钢弯头,铜弯头,铝合金弯头等.高压弯头是管道安装中常用的一种连接用管件,用于管道拐弯处的连接.其他名称:90度弯头,直角弯,爱而弯高压弯头的基本工艺过程是:首先焊接一个横截面为多边形的多棱环壳或两端封闭的多棱扇形壳,内部冲满压力介质后,施以内压,在内压作用下横截面由多边形逐渐变成圆,*终成为一个圆形环壳.根据需要,一个圆形环壳可以切割成4个90°弯头或6个60°弯头或其它规格的弯头,该工艺适用于制造弯头中径与弯头内径比大于1.5的任何规格大型弯头,是目前制造大型高压弯头的理想方法.牛角芯棒式热推弯头,弯头的弯曲半径R=(1~2)D(R是弯曲半径,D是弯头直径),芯棒式热推弯工艺具有如下优点:(1)工艺简单、生产率高,能满足大批量生产的要求。(2)该工艺可以避免传统弯管工艺成形时,管壁凸边受拉减薄、管壁凹边受压增厚而造成的弯管壁厚不均匀现象。(3)采用该工艺可以推制出壁厚均匀的大半径、厚壁(t/D≥0.015)弯头,其中t是厚度,D是管坯直径,这是其它弯管工艺无法实现的。(4)出于推弯过程中轴向处于压力状态,使金属***致密,故所得弯头力学性能良好。一些管材的材质要求热弯,从而可以获得良好的机械性能;(5)采用该工艺可在同一牛角芯棒上一次推制出相同口径的等多种弯曲角度的弯管,生产效率高。(6)由于加热迅速,热效率高,故弯头表面氧化皮少。缺点是不能形成带直段的弯头,中频感应加热机组耗电量大,设备***也大。牛角芯棒的形状较复杂,没有准确的计算公式,所以制造较困难,而且需要专用的卧式推制机。无缝高压弯头的材质通常采用优质的铸钢、不锈钢或合金钢,能够使高压弯头在各种高压管道中承受高压并能承受管道中流体的腐蚀。不仅需要具备良好的抗压能力,在不同的管道系统中还需要具备其他的优良特性。比如,在混凝土输送管道,泥浆输送管道中的高压弯头不仅要能承受起较高的管道压力,还必须具有良好的耐磨性能。而在输送管道系统中的高压弯头,除了要承受较高的管道压力外,还必须具有抗腐蚀和抗酸碱能力。国标无缝弯头成形工艺是采用专用弯头推制机、芯模和加热装置,使套在模具上的坯料在推制机的推动下向前运动,在运动中被加热、扩径并弯曲成形的过程。管坯摆放在下模上,将内芯及端模装入管坯,上模向下运动开始压制,通过外模的约束和内模的支撑作用使弯头成形。与热推工艺相比,冲压成形的外观质量不如前者。除上述三种常用的成形工艺以外,无缝弯头成形还有采用将管坯挤压到外模后,再通过管坯内通球的成形工艺。但这种工艺相对复杂、操作麻烦,且成形质量不如前述工艺,故较少采用。按照度数可以分为45度20g弯头,90度20g弯头和180度20g弯头。大口径对焊弯头按照角度可以分为45度大口径弯头,有90度大口径弯头和180度大口径弯头及其它不同的角度的弯头。按照材质可以分为碳钢大口径弯头,不锈钢大口径弯头,合金钢大口径弯头。按照的曲率半径可分为长半径大口径弯头和短半径大口径弯头。弯头是用一个标准的弯头坯剪裁成一个V形口的弯头,然后施压,借助于常规或专用冲压设备的动力,使弯头坯在模具里直接受到变形力并进行变形,从而获得一定形状,尺寸和性能的产品零件的生产技术,慢慢的在施压作用下逐渐变成圆,成为一个圆形环壳,焊接成型,然后用弯头设备就大功告成了。管坯,模具和设备是异径弯头加工的三要素。异径弯头加工是一种金属冷变形加工方法。180度无缝弯头生产厂家无缝弯头管件的原料是圆管坯,圆管胚要经过切割机的切割加工成长度约为一米的坯料,并经传送带送到熔炉内加热。钢坯被送入熔炉内加热,温度大约为1200摄氏度。炉内温度控制是关键性的问题.圆管坯出炉后要经过压力穿孔机进行穿空。一般较常见的穿孔机是锥形辊穿孔机,这种穿孔机生产效率高,产品质量好,穿孔扩径量大,可穿多种管件。穿孔后,圆管坯就先后被三辊斜轧、连轧或挤压。挤压后要脱管定径。定径机通过锥形钻头高速旋转入钢胚打孔,形成管件。180度长弯头适用介质为气体、液体、蒸汽;被广泛用于石油,化工,电利,建筑,水利等各种大型工程.产品质量符合出口及***执行产品高压管件产品标准.产品工艺标准及质量控制:进料-理化-下料-热锻成型-热处理-检验-金加工-成品检验-标识-成品检验-标识-包装打字-发运.)