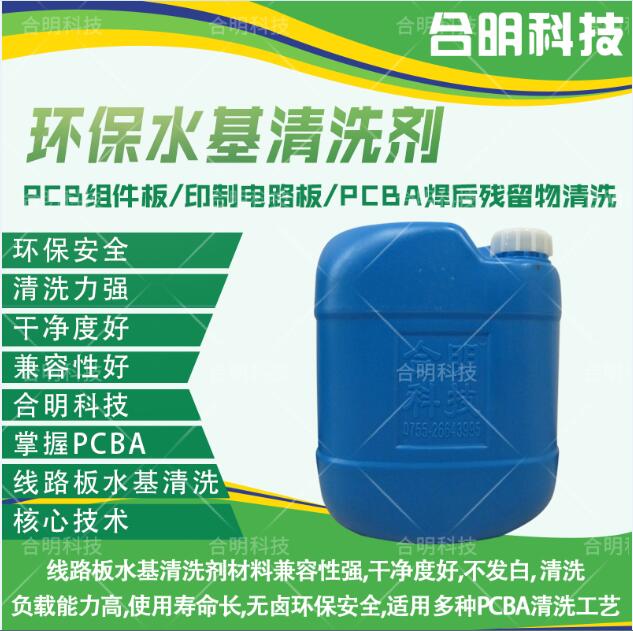
碱性的PCBA线路板清洗剂 线路板水基清洗剂 合明科技
导致白色残留物形成的机理有以下几种因素:1、热氧化:松香在温度超过200℃时,可能经历热氧化。松香的热氧化减少松香酸的不饱和双键。不饱和双键的减少会导致乙二醇、酮和不同分子量的酯的形成。这些残留物会在表面逐渐消失,并氧化进入粘牢的白色残留物里面。焦的残留物分布在助焊剂的周围,也散布到焊料凸点上。在这两个位置上的助焊剂膜都较薄,并且更易于氧化和变焦。氧化现象在单板吸收多热量的部分是很普遍的。有接地面的多层板在离电路组件的地方吸热,因此需要更高的再流温度曲线。相似的结果发生在焊接面阵列元器件及晶片电容s。由于热点烧焦了助焊剂残留物,这些小型元器件底下的残留物趋向于以不规则形状的形式进行氧化。2、聚合作用:温度超过200℃时,会导致松香和树脂结构的聚合。聚合作用的发生是加热的结果,金属盐扮演催化剂的角色,提高化学反应的速率,形成三维网络的聚合物链。链增长的化合物连接双键,加入到树脂化合物中,形成一条重复的链。3、使用低残留免清洗助焊剂的阻焊膜吸收:当使用干膜阻焊膜及低残留助焊剂时,湿气的吸收是很有影响的。波峰焊助焊剂和热量会分解,并使干膜掩膜膨胀。这可能是由于单板制造时粘性固化和终固化引起的。当单板经过预热区和焊料波峰时,干膜上的气孔张开并扩展。低残留助焊剂中的挥发性溶剂被吸收进阻焊膜里。单板表面过波峰焊后,掩膜形成了一种白色残留物。白色混浊斑点通过将热风返修工具的温度设定在400℃(752F)去除。温度会使低残留助焊剂活化并去除白色膜。助焊剂的种类、形态及经过焊接高温后残留物的可变性,都不同程度的决定了残留物的清洗难度。每种助焊剂因其不同的化学组成,在焊接过程中可能发生高温氧化、聚合、分解及与金属盐的结合反应等,导致残留物可能发生固塑性等可变性,增加或改变残留物的可清洗性。清洗剂效果一种清洗剂的选择应基于清洗效率、材料兼容性、每块产出单板的化学成本以及对环境的影响。元器件问题和残留物复杂的元器件几何形状、狭小的器件托高高度、非密封封装的元器件可能夹裹的清洗液和湿气,都有可能影响清洗过程和物料通过率。元器件上的残留物可能以颗粒、油或者膜的形式在组装操作前被发现,这些残留物在焊接后可能会一直存在于清洗的或未清洗(免清洗)的组件中。组装残留物清洗过程的敏***应该考虑如:金属表面处理、低温塑料、擦拭布或者其他暴露的电器插头及其他材料,能依赖于清洗剂膨胀。如某些特定的元器件,不是为可生产性设计的,不具备可清洗性时,清洗选择会受到限制。其他要点组装残留物的清洗还应考虑除去助焊剂、清洗剂、及元器件之外的其他要点,如:人工手工作业引入的污染物、可去除的不干胶标签、元器件包装(如以编带卷轴、托盘或者管装形式)、暂时性阻焊材料、润滑油和油脂、粘合剂、工作场所和周围储存条件。对于常见的普遍电路板PCBA,合明科技则采用中等强度的清洗剂,其满足业内普通线路板的材料兼容性,其清洗力属较好,能满足绝大部分的线路板清洗需求(一)基板:设计清洗工艺的步是印制线路板布局的审查以确定镀覆孔,孔的厚径比,任何适用堵塞或掩蔽的导通孔,和阻焊膜材料的选择。部件组成、尺寸和几何形状可以创造低间隙和小出口的夹层元器件而导致残留很难去除。小型和轻量的部件当它们通过清洗工艺时增加了夹持组件的需求。清洗工艺设计首先考虑电路板表面、金属化和兼容性的限制。部件的限制可能会使一些元器件在进行清洗工艺时受到限制。所有电路板设计都必须考虑这些再流焊因素及参数的重要性。溶剂包含不同类型的分子间相互作用:氢键、离子偶极和偶极间吸引。随着助焊剂残留物改变,清洗速率也有所不同。对于所有清洗活动,清洗剂和清洗系统-包括时间、温度和力度都会影响清洗效果。)