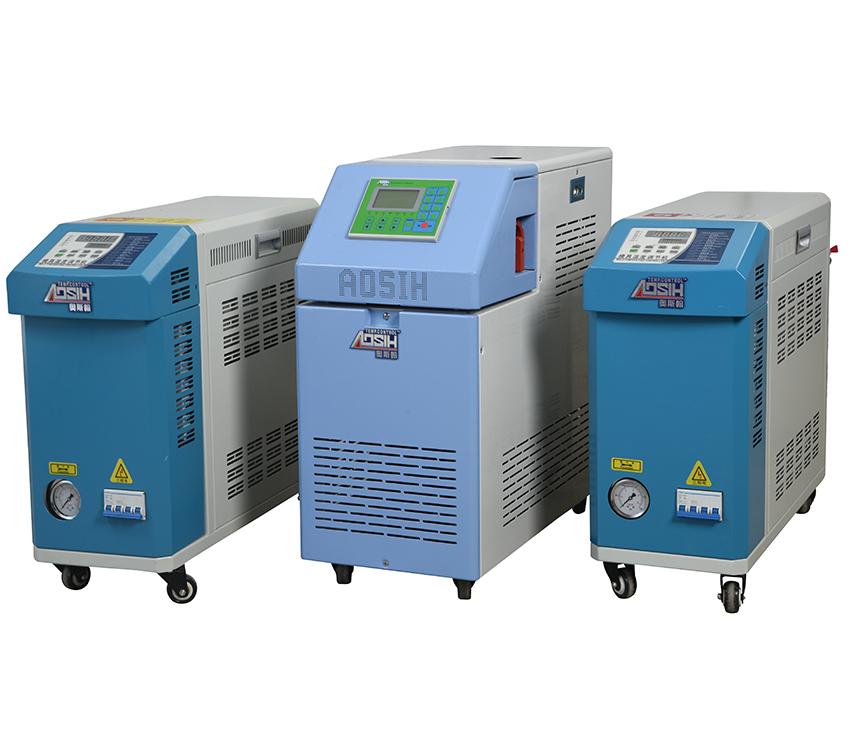
佛山水式模温机厂家-鸿锋成
油式模温机是现代多数大型企业经常使用的工业控温设备,但为什么不同用户的油式模温机使用寿命存在着较大的区别?这是因为大家在使用模温机的时候,对模温机的维护***是否到位。那么,如何延长油式模温机的使用寿命呢?1、对于新的油式模温机,要根据使用温度定期更换导热油,对于200℃以上的,要定期看油有没有少,五至六个月更换一次,而200℃以下的我们则可以一个1年更换一次,这样就很好避免了结垢的问题。2、制定模温机的清洁***的规章制度,对每次进行的***工作进行记录。对机组进行清洁时,不仅仅是对外观的一个清洁,更主要的是每年度要对机组的电器元件、过滤器、阀门等都要做好清洁工作,以免水质中的杂质结垢影响模温机正常运行。3、在使用模温机时,操作人员应时刻注意机组的使用。要是循环泵浦出现异常声音或是什么故障时,我们一定要先及时关机,防止电机收到损坏。并且根据模温机控制面板中的故障提示进行故障排除,在故障还没有排除之时,切记不可启动模温机。4、根据油式模温机的使用时间,更换导热油。导热油做为模温机的传热介质,其性能影响模温机的工作效率。如果导热油出现积碳严重,不仅会影响发热管的使用寿命,还会造成费电,建议在每半年检查一次导热油的情况,及时更换。5、模温机操作人员应该定期做好机组运行时的各项数据的记录,以方便以后的查询,在长时间使用后要对机组各部件进行检查,确保能够正常工作。在模温机长时间不需要运行时,应该将机组内部及管道的导热油清理干净,避免损坏机组部件。6、每次使用完模温机,简单对其进行清理打扫,避免积尘过多,影响模温机的操控。总是,定期清洁***油式模温机,可以延长起使用寿命。除此之外,模温机合理正确的操作非常重要,这不仅关系到模温机设备性能,更关系到设备及人身的安全,因此对于模温机的操作要小心谨慎,按照说明书进行操作和维护,来延长模温机的使用寿命。由于镁合金的铸造性能如流动性对模具温度和浇注温度相当敏感,在充型过程中,镁合金液极易凝固,因此为了保证镁合金压铸件的表面和内在质量,降低压铸生产的废品率,提高压铸的生产率,同时提高压铸模的使用寿命,必须***地控制压铸模具温度。为了满足镁合金压铸加工的需要,有必要研制压铸模具控温的设备。一、模具温度控制功能要求在镁合金压铸生产中,根据其生产特点,压铸模的温度控制包括模具的预热和冷却两个方面。温度与压铸的材料有关,也与压铸件的尺寸有关,一般为浇注温度的1/3左右,对于镁合金,通常为180~280℃。此外,在预热过程中,应尽量使模具的各部分均匀加热,避免剧烈地加热和局部过热对模具的使用寿命带来的不利影响。一般情况下,模具吸收的热量要大于自然散热量,因此随着压铸生产进行,模具的温度会越来越高。为了进行正常的压铸生产,必须维持模具的温度基本恒定。一般通过在模具中开冷却水道并通冷却水对模具进行冷却。由上所述,为了对模具进行预热和冷却的恒温控制,可以采用导压铸专用模温机对模具进行控温,导热油不间断地通过模具内部管道,从内部对模具进行加热或冷却,使模具维持一定的温度,处于合适的生产状态。二、压铸专用模温机控温原理压铸专用模温机采用导热油循环控温,当导热油在模具的冷却通道中循环流动时,由于导热油和模具通道壁(模具)之间存在温差,它们之间存在着热量的传递。热交换量与导热油的热力学性能、模具通道截面积、导热油流量、油温、模温等因素有关。在确定了导热油型号、模具通道截面积后,热交换量可用牛顿冷却公式φ=Ah(Tm-Tf)来计算,其中,φ为系统的热流量,A为换热表面面积,Tm为模具温度,Tf为导热油温度,h为模具内部流体通道的平均表面传热系数,与导热油流速有关。由于模具通道截面积已确定,导热油流速可由导热油流量计算确定。故系统的热交换量可由下述的函数关系式表示:φ=f(q,Tm,Tf)式中,q为导热油流量,m³/s。模具温度Tm是被控制量,希望能保持恒定,即Tm基本是一个常数。因此,只要控制导热油流量q或导热油温Tf,在一定范围内,即可控制它们之间的换热量,从而控制模具的加热和冷却,进而控制模具的温度。为控制方便起见,可采用固定导热油流量调整导热油温度的方法,这样只要控制好导热油的温度即可控制压铸模具的温度。模具的热交换通道与模具温控杌的循环油泵、阀、管路、加热器、冷却器等部件一起构成一个完整的导热油循环通路,除模具外,其他部件都进行隔热保温处理。高温油泵将导热油吸人循环通路,控制系统控制导热油在要求的温度下进行循环。当油温低于设定的温度时,系统对导热油进行加热,升高油温到设定的温度;当油温高于设定温度时,打开冷却水控制电磁阀,降低油温到设定的温度。三、系统关键部件的选购与设计压铸专用模温机中***关键的外购件是高温导热油泵,对油泵的基本要求是在高温导热油的作用下,油泵仍能正常工作且具有良好的密封性。此外,应根据设计的要求,由模具的热平衡核算模具冷却时需由导热油带走的热量值,计算出所需的导热油流量,根据导热油流量的大小,选择相应的高温油泵。压铸专用模温机的设计主要是考虑满足对模具预热的要求。加热器的外部必须包上一层足够厚的绝热材料,以减少热损失。在不考虑温控机本身循环通路的散热情况下,可根据模具的大小、升温的时间以及模具自身的散热对加热功率进行相应的计算。根据计算结果,选用相应功率的棒状加热器。在加工时,可将加热棒与多根细油管通过铸铝形成一个整体,这样可以保证加热均匀、快速,同时避免过热造成导热油的碳化。压铸专用模温机冷却器的设计主要是满足模具散热的要求。对模具进行热平衡核算,得到需由导热油带走的热量,这些热量通过冷却器进行热交换,由冷却水带走。冷却器设计成套管式换热器,冷却水在内管内流过,导热油在内管和外壳之间的夹层中流过。套管式换热器加工制造简单,但是套管式换热器的换热面较小,传热量不大,因此在使用中可以根据需要将两个或更多的套管式换热器串联起来,形成多管程和多壳程的换热器,满足设计和使用要求。另外压铸专用模温机都必须保证在高温导热油的作用下处处严格密封,否则,会在机件表面产生较大的烟雾,对车间的工作环境产生不利影响。四、控制系统开发压铸专用模温机的控制系统由PLC、人机界面显示器、传感器以及相应的执行元件组成。系统采用西门子PLC作为核心控制器,完成各种类型的开关量输入信号检测、传感器信号检测以及控制信号输出等。在生产过程中,人机界面显示器通过与PLC通讯,将PLC采集到的数据送到人机界面显示器中,实时显示系统工作状态,并将用户设置的参数(如温度)发送到PLC中实现用户参数设定。压铸专用模温机采用电阻式加热器,加热时采用固态继电器过零触发的调功控制方式;系统冷却时采用接通电磁阀通冷却水降温的控制方式。在控制算法上,采用模糊控制进行温度控制。由于生产中压铸模具和压铸件大小不一、尺寸各异,且不时要更换模具,温度控制中经常采用的PID算法有较大的局限性,必须根据不同的模具整定不同的控制参数,这很不方便。因此在算法设计上,模具的控温采用模糊控制。在模具升温过程初期,采用全功率输出,以使模具迅速升温,当模具温度达到设定温度的80%左右时,系统对输出变量(即输出功率)采用模糊控制方式,避免系统产生较大的超调;在连续压铸进行降温控制时,系统同样采用模糊控制算法对冷却水控制电磁阀的通断进行控制,维持模具的温度在某一预先设定的温度。由于固态继电器的调功和冷却水控制电磁阀的通断都是开关的方式,系统将模糊运算的结果进行转化,使其输出为周期固定,占空比可调的方波,形成所需的控制信号。这种控制方法对不同尺寸大小的模具具有良好的适应性,在设定的模具温度上保持较高的稳定性和***性。)